IN BRIEF
|
Connecting a Mitsubishi Electric PLC to a SCADA network is a critical aspect of industrial automation that allows for enhanced monitoring and control of various processes. This integration enables real-time data exchange and operational visibility, thus streamlining production efficiency. The process typically involves establishing communication protocols that facilitate smooth data transfer between the PLC and the SCADA system. Mitsubishi Electric provides several software tools and methodologies to aid in this integration. Utilizing the appropriate protocols, such as Ethernet or RS232, and ensuring compatibility with SCADA software like MC Works64 or GENESIS64™, are essential steps for achieving a robust connection. Understanding these components ensures that engineers can effectively implement a seamless connection, maximizing the capabilities of the SCADA system and the PLC alike.
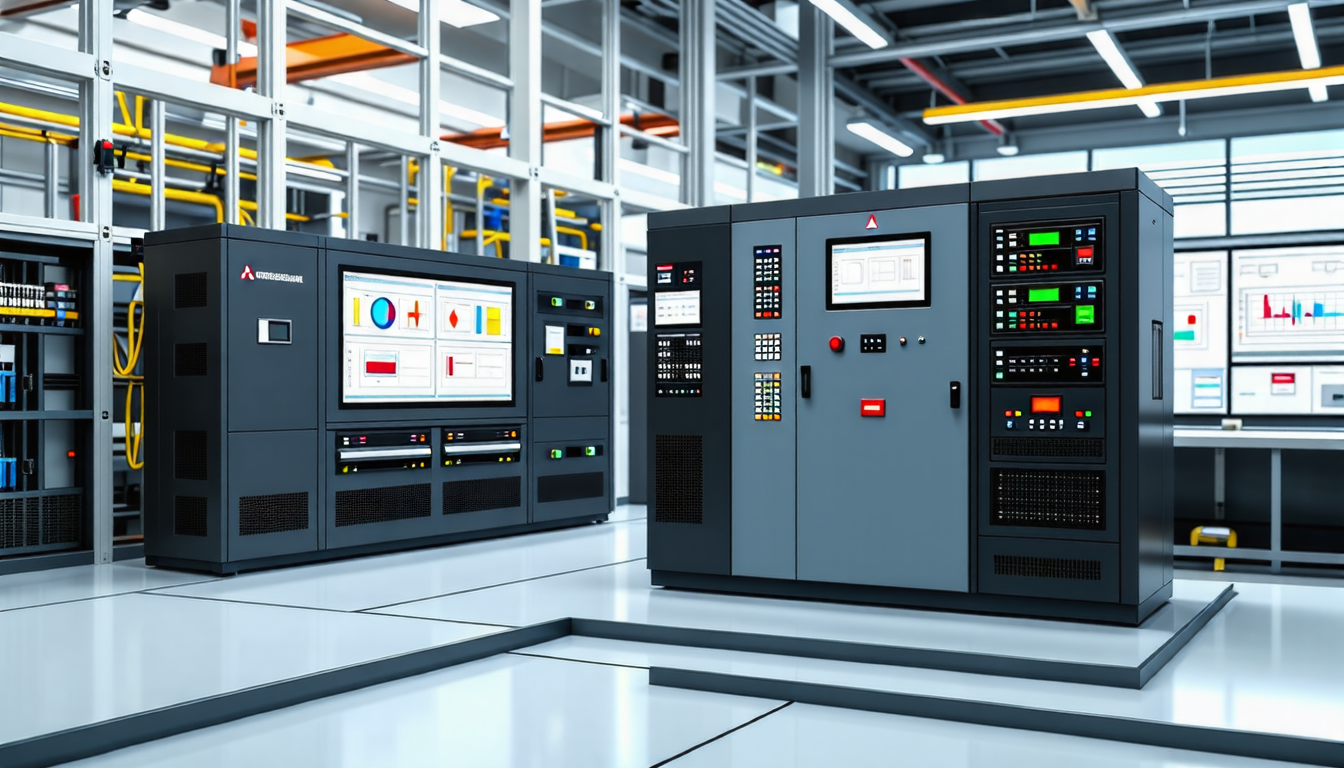
Establishing a robust connection between a Mitsubishi Electric PLC and a SCADA network is essential for optimizing industrial automation processes. The integration enables real-time monitoring and control over various industrial operations, enhancing efficiency and decision-making. Various methods can facilitate this connection, depending on the specific PLC model and its network capabilities.
Enhancing Communication with Advanced Protocols
For organizations seeking to optimize performance further, exploring advanced communication protocols can unlock additional functionality. Utilizing protocols such as MELSECNET/H can enhance communication networks, allowing for direct connections of PCs for SCADA and maintenance applications. This capacity empowers more sophisticated system architectures and improves the response time for real-time applications.
Bridging Different Networks
If integrating different types of protocols, such as CC-Link back to Ethernet-connected PLCs, it is essential to establish a clear bridging method. With the right configuration, networking devices can create a seamless communication channel between distinct PLC architectures, ensuring that the diverse systems work cohesively within the SCADA framework.
Employing Visualization Tools
SCADA systems offer visualization capabilities that enhance operational insight. Advanced SCADA software, like GENESIS64™, provides functionalities such as real-time analytics, mobility options, and expanded connectivity, allowing users to gain a contextualized view of their operations. These tools maximize the utility of the collected data and facilitate informed decision-making in critical situations.
Connecting a Mitsubishi Electric PLC to a SCADA network involves a series of precise steps to ensure seamless integration and effective communication. First, determine the appropriate communication protocols, such as Ethernet or RS232, and configure the necessary settings in the PLC and SCADA software. Utilizing options like MELSECNET/H allows for efficient network connectivity while ensuring direct access to PCs for monitoring and maintenance. It is essential to verify compatible OPC servers when using SCADA software like MC Works64 to facilitate a reliable data exchange. The careful selection of communication modules and software will lead to a successful and functional PLC-SCADA interface.
FAQ: Connecting a Mitsubishi Electric PLC to a SCADA Network
What is the first step to connect a Mitsubishi Electric PLC to a SCADA network? The initial step is to ensure that the PLC is properly configured and powered on. It’s essential to have the correct network settings established before attempting any connections.
Which communication protocols are compatible with Mitsubishi PLCs for SCADA integration? Mitsubishi PLCs support various communication protocols, including Ethernet, RS232, and CC-Link. Select the appropriate protocol based on your SCADA system requirements.
How can I establish a connection between the PLC and SCADA software? You can connect the PLC to the SCADA software by using an OPC server. Ensure compatibility with the Mitsubishi PLC and the SCADA system in use.
What software is recommended for programming Mitsubishi PLCs? The recommended software is GX Works2 for programming various Mitsubishi PLC models, including the A2C controller.
Is it possible to connect multiple I/O modules to the Mitsubishi PLC? Yes, Mitsubishi PLCs can accommodate multiple I/O modules, allowing for extensive input and output options depending on the application needs.
What should I do if I face communication issues between the PLC and SCADA? First, verify the cabling and connections. If issues persist, you may need to check the network configuration settings or examine if the firewall settings are blocking the communication.
Can I use remote access to connect to my Mitsubishi PLC in a SCADA environment? Yes, remote access is achievable by using VPN or incorporating a cloud-based interface, depending on the SCADA software capabilities.
How do I specify the communication parameters in the SCADA system? In your SCADA software settings, navigate to the communication parameters section and enter the required details, such as IP address and protocol type related to the Mitsubishi PLC.
What troubleshooting steps should I take if the SCADA system does not recognize the PLC? Confirm the PLC is operational, ensure proper integration settings in the SCADA, and verify the linking parameters such as the device addresses and network protocols.