IN BRIEF
|
When faced with challenges in a Mitsubishi Electric programmable logic controller (PLC), effective troubleshooting is essential to ensure optimal performance and minimal downtime. The complexity of PLC systems can lead to various issues, including communication failures, hardware malfunctions, and programming errors. To address these challenges, it’s crucial to start with a thorough understanding of the PLC’s components and functionalities. This involves examining the power supply, checking for loose connections, and reviewing the ladder logic programming if needed. Developing a systematic approach to troubleshooting not only enhances the technician’s efficiency but also aids in swiftly identifying the root causes of problems. By following established techniques and applying practical knowledge, technicians can effectively navigate the intricacies of Mitsubishi Electric PLC systems, leading to timely resolutions and sustained operational integrity.
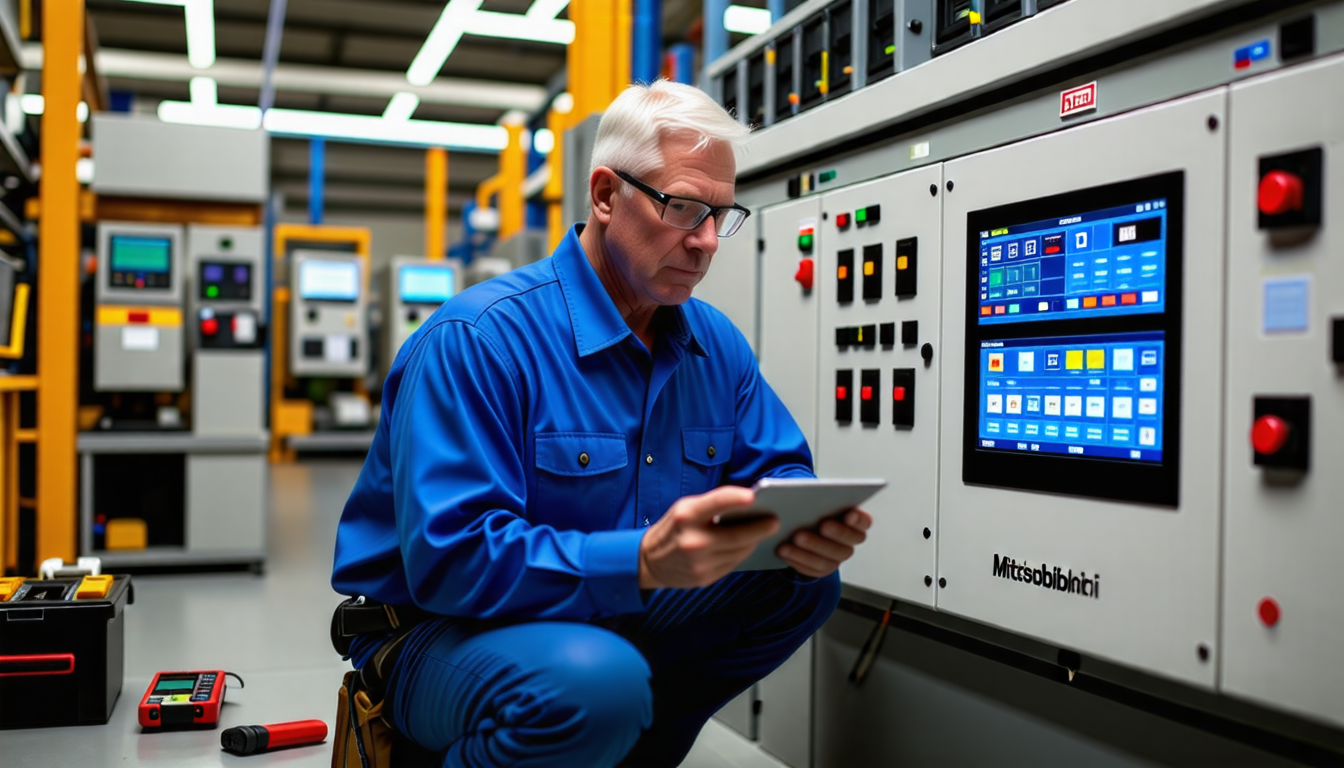
Understanding the Basics of Mitsubishi Electric PLCs
Programmable Logic Controllers (PLCs) are essential components in industrial automation. Mitsubishi Electric PLCs, known for their reliability and advanced functionality, require a solid understanding of their basics for effective troubleshooting. These devices operate through input and output modules that interact with various sensors and actuators in an industrial environment. Having a grasp of these fundamentals sets the stage for identifying and resolving issues swiftly.
Ensuring Proper Power Supply
A crucial first step in troubleshooting any Mitsubishi Electric PLC is to confirm that it is receiving adequate power. The power supply must be sufficient to support all connected loads. If the PLC appears unresponsive, inspect the transformer connections and fuses for any signs of damage or failure. A thorough examination for loose connections can prevent power-related issues that often cause system malfunctions. If everything checks out but the PLC remains non-operational, further investigation into the hardware may be necessary.
Examining Control Circuit Integrity
Once power integrity is confirmed, attention should shift to the control circuit. Inspect the physical wiring for damage, wear, or corrosion which could lead to signal loss. Verifying that all wiring adheres to the manufacturer’s specifications is crucial. Additionally, consult the installation manual to ensure correct connections. Any discrepancies could lead to malfunctioning hardware or communication problems.
Identifying and Correcting Programming Errors
Hardware issues often go hand-in-hand with programming errors. An empty program or a corrupted program can cause the PLC to enter an unintended operational state. Utilize programming software compatible with Mitsubishi Electric PLCs to upload the existing program and verify its integrity. If necessary, re-upload or reset the program to restore proper functionality. Make sure to check for any updates from the Mitsubishi website to maintain compliance with the latest programming standards.
Addressing Communication Failures
Communication issues can severely impact the effectiveness of your Mitsubishi PLC in coordinating with other devices. Look for faults in communication protocols, such as MODBUS or Ethernet, ensuring that all settings match across devices. Physical connections should be validated for damage, and all cables should be securely attached. For systems integrated with SCADA, reference the guide on connecting a Mitsubishi Electric PLC to SCADA networks. This resource can assist in troubleshooting complex network communication issues.
Utilizing Diagnostic Tools
Mitsubishi Electric provides various diagnostic tools to assist in troubleshooting. These tools often include software applications designed specifically for Mitsubishi PLCs, which can analyze and report system status in real time. Utilizing diagnostic software can facilitate faster identification of errors, providing clear insights into fault conditions. Being adept at using these tools enhances the ability to troubleshoot effectively.
Running Self-Diagnostics
Many Mitsubishi Electric PLCs come equipped with self-diagnostic features that can automatically check for common issues. Initiating self-diagnostics may yield errors or alerts directly indicating the underlying problem. Familiarize yourself with the specific PLC model’s capabilities and how to access these diagnostics. This proactive approach can save valuable time during troubleshooting.
Verifying System Components
Hardware components may also be the source of PLC issues. Sometimes, PLCs will exhibit problems due to malfunctions in I/O modules or outdated firmware. Inspect each component for signs of wear, overheating, or physical damage. If any components are suspected to be faulty, replacing them with verified parts is advisable to restore the system’s integrity and functionality.
Checking for Environmental Factors
Environmental conditions surrounding the PLC can significantly impact its performance. Factors such as overheating, humidity, and electromagnetic interference can deteriorate PLC performance. Ensure that the PLC is housed in a suitable environment, as outlined in the manufacturer’s guidelines. Address any issues stemming from the installation area to prevent future malfunctions.
Implementing Regular Maintenance Protocols
To enhance the longevity and reliability of Mitsubishi Electric PLCs, implementing a regular maintenance schedule is vital. This includes routine inspections, software updates, and hardware cleanings. The resource contains essential tips for maintaining Mitsubishi systems, which can be adapted for PLC care as well. Proactive maintenance can preempt many common issues before they escalate into major problems.
Documenting Issues and Solutions
Maintaining a log of problems and their respective solutions provides valuable insights into recurring issues. This documentation aids in identifying patterns that may not be immediately apparent but can flag potential weaknesses in the system. It serves as a crucial reference for anyone tasked with troubleshooting the PLC in the future.
Accessing Support Resources
If all troubleshooting efforts fail and the issue persists, it may be necessary to seek support from Mitsubishi Electric directly or through official channels. Utilize online forums, technical support lines, and user groups dedicated to Mitsubishi PLC products. Sharing your experiences and seeking advice can lead to discovering effective solutions that may not be documented elsewhere.
Utilizing Extended Modules
Sometimes, enhancing the PLC’s capabilities through additional modules can resolve specific functionality concerns. Understanding your options for expansion and how to correctly integrate these modules into your system can create efficiency gains and optimize performance. For insights into available extensions, guide yourself through resources such as an overview of extension modules.
Finding Solutions to Common PLC Problems
It is also invaluable to be aware of many common PLC faults and their associated troubleshooting procedures. Issues such as communication breakdowns, I/O errors, and processor malfunctions happen frequently, yet they can often be quickly resolved with a firm understanding of the system architecture and operational logic.
Utilizing Flowcharts for Troubleshooting
Visual aids such as troubleshooting flowcharts can provide quick reference points to follow when diagnosing issues. These can guide technicians through a systematic approach to problem-solving, ensuring that no steps are overlooked. Familiarity with a PLC troubleshooting flowchart improves diagnostic efficiency and response times during emergencies.
Understanding Error Codes
Mitsubishi Electric PLCs often display error codes that can provide immediate insight into the nature of an issue. Maintaining a comprehensive understanding of these error codes, their meanings, and potential solutions can dramatically streamline the troubleshooting process. Regularly review documentation associated with the specific PLC model and refer to it to quickly resolve operational dilemmas.
Leveraging Training Resources
Ongoing education is essential for staying current with PLC technology and troubleshooting practices. Mitsubishi offers extensive training programs designed to enhance users’ capabilities in handling PLC operations. Engaging in these training sessions can provide deeper insights into effective troubleshooting methods, empowering technicians to act with greater proficiency.
Final Thoughts on Effective Troubleshooting
The effectiveness of troubleshooting Mitsubishi Electric PLCs is dependent on a structured approach: understanding basic functionalities, ensuring power integrity, verifying components, and utilizing available support resources. Keeping abreast of common issues, continuously updating skills through training, and maintaining thorough documentation are essential practices for achieving operational excellence in industrial automation environments.
Successfully troubleshooting a Mitsubishi Electric programmable logic controller (PLC) requires a systematic approach. Start by confirming that the PLC receives adequate power from the transformer to support all connected loads. Assess the hardware for any signs of malfunction, including loose connections or damaged components. Additionally, examine the programming to ensure there are no errors that could impede operation. Communication issues may also arise, necessitating a review of network configurations. By following a structured troubleshooting process, you can effectively identify and resolve common PLC issues, ensuring optimal performance of the automation systems in place.
Frequently Asked Questions about Troubleshooting Mitsubishi Electric PLCs
What should I check first when troubleshooting a Mitsubishi Electric PLC?
Begin by verifying that the PLC is receiving adequate power from the transformer. Ensure that all loads are properly supplied with energy.
What are common causes of faults in PLCs?
Faults can arise from several sources, such as poor wiring, incorrect programming, hardware malfunctions, and communication problems.
How can I determine if the program in the PLC is lost?
If the PLC is not functioning properly, it might be due to a lost or reset program. In this scenario, an empty program may be preventing the PLC from entering run mode.
What steps should I follow to troubleshoot PLC hardware?
Start by reviewing both the PLC hardware and the associated program. Understand the current state to ascertain what is occurring and the potential reasons behind it.
What should I do if the PLC loses track of time?
If the PLC is unable to keep accurate time, check if the battery is exhausted. Replacing the battery may resolve this issue.
How can I fix communication issues between the PLC and other devices?
To troubleshoot communication problems, ensure all connections are secure and verify that configurations are correct between the PLC and associated devices.
Are there visual aids that can assist in troubleshooting?
Utilizing a troubleshooting flowchart can guide you through the diagnostic process, helping to identify common issues and their solutions based on symptoms observed.
What are some best practices for maintaining a Mitsubishi Electric PLC?
Regular checks on power supply, timely updates on existing programs, and routine inspections for loose connections or burnt fuses are essential in maintaining optimal PLC performance.